The IoT’s impact on supply chain management
From a technical viewpoint, it’s easy enough to name the benefits of the IoT. Large arrays of low cost, low power, rugged sensors can gather detailed data from any type of natural, industrial or commercial process, while powerful cloud-based computer resources crunch this data to extract actionable information.
But how can organisations best exploit this unprecedently powerful and fast-evolving tool? How can they gain deep new insights that will allow them to not only improve their service to their customers, but also the products they are manufacturing – in terms of both quality and alignment with what the customer really wants?
In this article we examine this question in terms of a resource that every business must have – a supply chain. While this is obvious where physical goods are involved, in the IoT world it’s also true when services or software products are being supplied.
We start by defining what a supply chain has come to mean today, then look at the elements within this chain and how these can, as suggested above, gain new insights that allow suppliers to improve both their services and their products.
Today’s supply chains
For manufacturing companies, whether their product is apparel, computers or something else, the supply chain starts with their raw material and/or component suppliers. Buffering between these incoming goods and the company’s production schedule is handled by a smart warehouse working with a flexible and smart production line. Finished goods then travel from the manufacturing plant to the company’s customers, who would typically be retail outlets or fulfilment warehouses. From here, the chain fans out to single shipments for individual end-users.
In pre-IoT days, the process would stop there. Apart from asking for customer feedback, which is usually patchy and limited, suppliers had no real visibility of what happened to their goods after end customer delivery. How did their users get on with them, did they meet their expectations and how could they be improved? How about when goods are consumed – for example, spikes in vending machine soft drink sales before a football match or popular TV programme.
Now we’ll take a closer look at how the IoT is helping businesses get more from their supply chain – firstly in improving track and trace, product quality monitoring and enabling granularity of customer choice, and then in gaining visibility of events after delivery to the end customer - and how this can feed back ultimately into an improved customer experience.
Upping the game – faster, more personalised deliveries
In a recent, well-publicised move, Amazon acquired Whole Foods for $13.7b. This acquisition makes perfect logical sense; while Amazon has succeeded in dramatically reducing delivery times compared with competitive offerings, it was still challenged to complete deliveries quickly enough to keep perishable food fresh. To achieve this, it needed a presence closer to its customers – and Whole Foods provided the solution . Its hundreds of stores offer a hyper-local presence in areas with the greatest density of high net worth individuals, so providing a perfect complement to Amazon’s on-line-driven delivery machine.
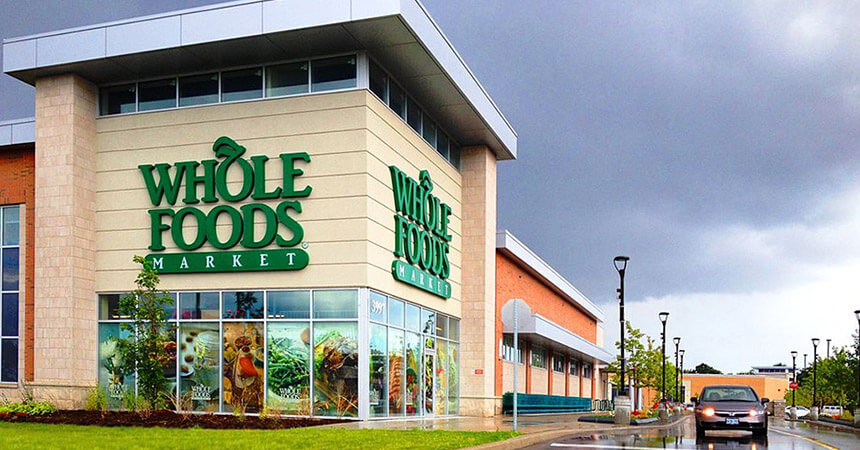
Fig.1: Whole Foods ‘Bricks & Mortar’ outlet – Image via Wikimedia Commons
While this is great news for customers, it increases pressure on competing suppliers who must now comply with a new level of expectations. In fact, this is just one aspect of today’s heightened expectations; customers want their products not only to arrive fast, but also to be configured exactly to their individual specification - and these requirements are typically set against a background of high production volumes. This trend comes from the retail sector, which has for a while been rolling out mobile apps that offer more tailored product choices . Sportswear maker Adidas, for example, has created custom product lines that allow consumers to specify their own variations on the standard SKU (Stock Keeping Unit).
Instead of a conventional purchase orders for tens of thousands of units at a time, those orders come into GT Nexus – a cloud-based collaboration platform used by Adidas - for single units, each with a custom bill of materials. It passes the order to the factory that makes the shoe, and instead of leaving the assembly line with just a SKU barcode, it also has the information needed to ship it to the customer, whether by sea or air. This calls for a so-called bimodal supply chain; optimised both for containers, and for single units of one.
This multimodal flexibility is coming to the B2B world too, as individuals buying the consumer goods are also managers in industrial companies, and bring their expectations with them. It’s a generic requirement, equally applicable across electronics, food & beverage, healthcare & pharmaceutical, automotive and other diverse industries. Implementing greater flexibility at speed often means re-evaluating how the supply chain is organised, because achieving these objectives may need a more modular approach. For example, a heavy equipment manufacturer may decide to build an incomplete base unit that ships from its factory, and then add certain parts to finish it off at a more local facility to meet individual customer specifications.
Segmenting the bill of materials across the supply chain in that way demands greater visibility. Instead of tracking entire container loads from the point of origin to a single destination, it may mean co-ordinating multiple journeys of individual items. That demands more instrumentation as units move through the supply chain, according to GT Nexus president Kurt Cavano. The company is involved in projects using IoT technology to provide what they call hyper-granular visibility into the supply chain; down to unit-of-one visibility, like the Adidas example. In their vision of the future, the supply chain becomes a continuous, real time process rather than a series of discrete steps.
From the viewpoint of a manufacturer or distributor, the supply chain comprises the warehouse and routes to the production line or order fulfilment floor, and the land, sea and air routes between the warehouse, suppliers, customers and end-users. In today’s complex, time-sensitive environment, the key challenges are how to track and trace products as they move through the chain, and how to ensure perishable food, pharmaceutical and other items remain fresh en route. Below, we look at these issues, and how IoT technology is being deployed to come up with solutions to meet modern realities.
Smart manufacturing and the supply chain
Demands on the supply chain are driven by its manufacturing ‘customers’. In fact, the two areas are becoming increasingly integrated and interdependent. In a Forwarder Magazine article , Lars Mohr Jensen, product manager at Gatehouse Logistics, discusses Industry 4.0, where manufacturing becomes intelligent. All individual steps in the production process will be fully connected and integrated. This will impact all planning, production and logistics processes in and around the factory, with processes driven by market needs for production cost reduction, faster time-to-market, mass production of individually configured products, and last-minute order changes. The IoT is effecting these developments by adding sensors to everything and connecting all in the manufacturing and supply chain.
In the car industry, for example, before any car is built, it is assigned a sensor tag, which can be assigned to a specific customer. The car then tells the robots along the production line how to build it. So, if a customer wants to change the specification for a satnav, they can – but it will impact on stock, on satnav suppliers and the whole smart supply chain.
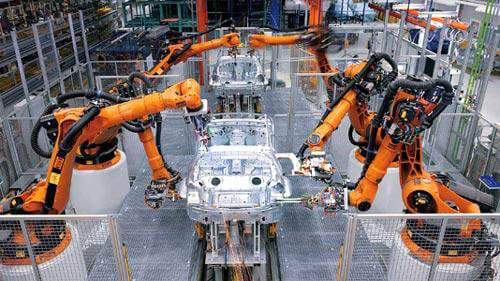
Fig.2: Industrial robots on the factory floor – Image via Wikimedia Commons
Transparency in the supply chain will be central to every smart factory in every corner of the world so that all know what goods are in transit and when they will be received.
But the smart logistics chain extends far beyond positional information of goods. It extends to conditional monitoring of data concerning every item en route to a smart factory. A smart factory needs to know if any satnav has been damaged when a truck went over a speed calmer, or if any have been exposed to excessively high temperatures or humidity, or other damaging circumstances in a trailer. This calls for islands of information from diverse platforms and systems being securely and transparently connected into one data cloud.
An innovative, smart warehouse solution
Above, we have mentioned today’s requirement for granularity of choice and efficient product handling in a fast, high volume production environment. One company with such requirements is Texas Instruments, whose Singapore-based Product Distribution Centre (PDC), with a capacity for storing 500 million semiconductors, was becoming overstretched. In response, TI installed a SwissLog AutoStore automated storage and order picking system that increases capacity to 2 billion parts within the same floor space. Productivity has increased by 40%, while inventory visibility and accuracy has been vastly improved.
Spanning 7,500 m2 of the 20,000 m2 facility, the AutoStore system comprises a massive three-dimensional grid measuring 65 m x 18 m x 5.4 m. The grid, which accommodates up to 63,000 bins to provide its 2 billion component capacity is 108 rows wide, 38 rows deep and is the height of 16 bins. Without need of aisles for movement of people and products, it offers significant space-saving.
Thirty-six robots ply the top of the grid to both store and retrieve products, based on orders placed through warehouse management software known as the AutoStore Control System (ACS). The ACS controls the entire inventory flow into and out of the AutoStore grid. Full visibility at any time is maintained as each item is electronically tagged. Backend information built into the system allows the robots to pick inventory based on the specific requirements of TI’s customers – for example, retrieving items manufactured within a specific date range.
More than 800 metres of light goods conveyor system connect the AutoStore grid to receiving and shipping areas, allowing for a swift flow of inbound and outbound goods within the PDC. Products arrive from 20 inbound countries and orders are consolidated and shipped to 54 outbound countries, complete with country-specific labelling created at the facility in Singapore.
Digitized supply chains over land and sea
Above, we have discussed how warehouse automation can supply a production line or distribution centre with customer-specific production kits at speed and in high volumes. However, such warehouses depend in turn on an effective long-distance logistics network that can handle all the complexities associated with the large numbers of suppliers, shippers and vehicles, component volumes and types, large distances and multitude of regions or countries where suppliers are located. It must also be resilient enough to handle unwanted events such as severe weather, theft, road closures, dock strikes, and human error.
There are issues of complexity for manufacturers of products such as cars or computers that require large lists of components. For food and pharmaceutical suppliers, timing is critical as their products can spoil rapidly if they suffer unexpected shipping delays.
Therefore, the challenge is to provide a logistics system that overcomes these issues while handling the fragmentation arising from the multitude of unrelated suppliers, shippers and other factors as mentioned.
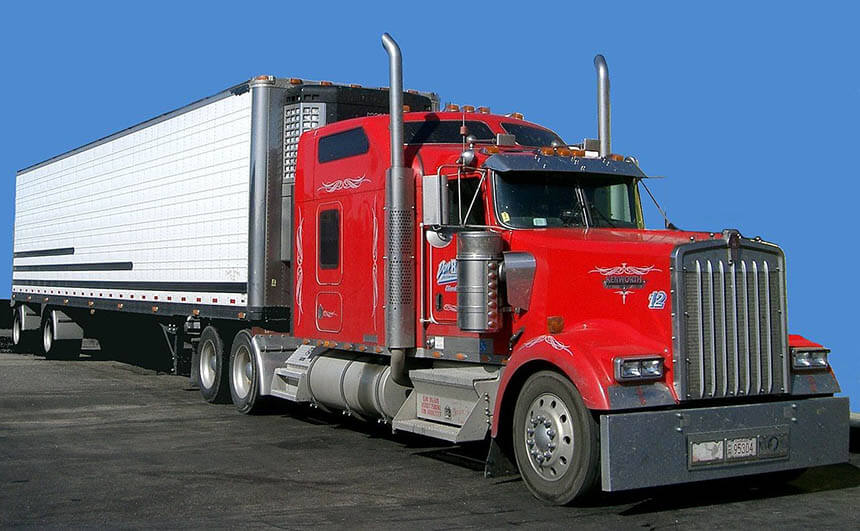
Fig.3: Trucks form part of a complex, time-sensitive logistics network – Image via Wikimedia - Commons
One approach, described in another article , employs Intel’s Smart Freight Technology, which uses IoT to bring more visibility to freight movement by attaching sensors to individual freight items, and vehicle-mounted gateways for tracking. Operators have a real-time view of where their products really are, not where a bar code scan thinks they might be.
But wouldn’t it be great if there were also a powerful resource to correctly monitor, track, correlate and provide transparency on all transactions from all participants – no matter how many there were, and how complex the trail of transactions? IBM and IT business solutions company AOS SAS have come up with a solution that integrates IBM’s Blockchain and Watson IoT. Blockchain is a shared, immutable ledger for transactions. It is large-scale, secure and resistant to fraud and error because it runs on multiple machines, with no single owner.
In the IBM blockchain supply chain application, relevant information is captured directly from sensors in the trucks, and entered into the blockchain, creating a single, shared repository that all authorised participants can access and which can only be altered by consensus from all parties. Input and output weight are captured to define available capacity, in addition to identifying which silo and person will carry the load. The data is then correlated against external information, such as weather, humidity, temperature and the driver’s data, providing customers with a much more accurate delivery time estimate.
Once the truck leaves the distribution point, an automatic message is sent to the customer, informing them about the load, weight and estimated time of arrival. If part of the delivery is returned, the invoicing can be automated depending on the actual load delivered. Also, through the sensors located on the trucks, an information repository is generated, which tracks all the exchanges, stops and transactions made by each truck and its respective load, from the distribution point to the final customer. This heightened level of transparency can help increase accountability between shippers and their customers, promoting the flow of business.
How customer feedback reduces losses in the perishable food supply chain
In a Customer Experience Report , Allen Proithis, president and co-founder of Internet of Things company wot.io, describes how combining IoT technology with customer feedback can improve product quality, for example by identifying and eliminating problems related to food spoilage during transit.
He explains: “Imagine that a call centre worker can pull up robust, real-time data on the supply chain that a product traveled from production to customer. Connected systems on the product floor, sensors in delivery trucks and in-store monitoring can give a clear picture of exactly that single product experience – and ultimately, identify where something went wrong, such as sitting on the truck too long, that caused multiple customer complaints,” he said.
He cited the example of a caller complaining about a food product. The IoT, he said, can help you see exactly the path from farm to table so that the call centre agent knows, for example, that the product was sitting on the truck for longer than it should have been. “It allows you to track a product through its entire lifecycle,” Proithis said. “This means that when a customer contacts an agent the information available is not just account and purchase history but the history of the product or service purchased.”
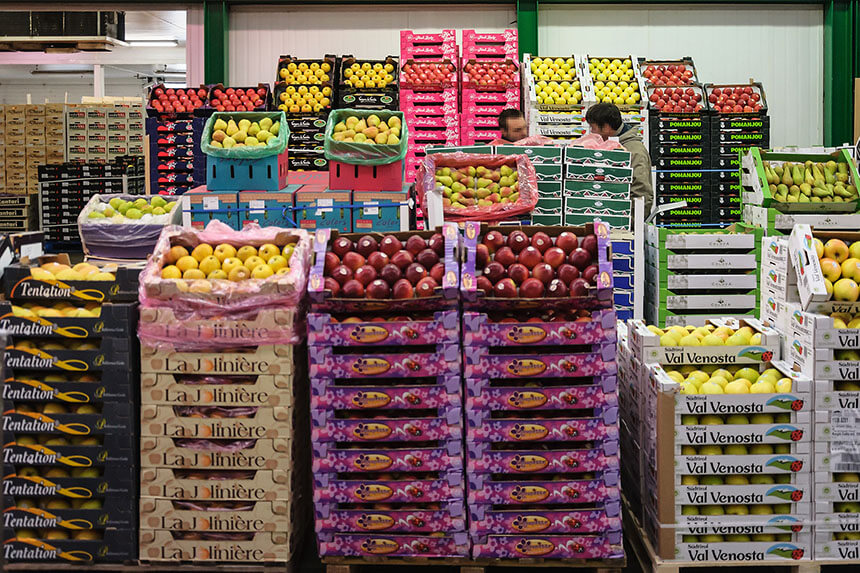
Fig. 4: Perishable food needs fast and careful transit – Image via Wikimedia Commons
After the product reaches the customer: Using feedback to improve service and design
An article by CITO Research describes how the IoT is shaping the future of customer experience and product development, by vastly accelerating product R&D. By using sensor, diagnostic, and user interaction data from devices, companies get full product transparency. By seeing how customers are using their products, businesses can quickly update features or adjust future models to more closely align with customer desires and behaviours. They can also better anticipate where consumer preferences are going in the future. This insight is invaluable – rather than going through tedious trial and error, companies can know in real time what is working and what is not, enabling organizations to make data-driven decisions and immediately react to correct or adjust issues. This leads to better product design—both now and in the future. For instance, iRhythm, a manufacturer of patches that can detect heart problems, leverages its devices to better understand use and ensure that its products operate as intended.
Customer service improves with access to this level of detail. Proactive notification of customers affected by an outage or affected device changes the paradigm of customer service. Companies can also then better position their customer support centres to allow more immediate service, reducing costs and appeasing customers simultaneously.
This virtuous feedback loop extends to the channels and methods organizations can use to interact with their customers. With the data from connected devices, companies can better understand and predict their customers’ preferences. Thus, rather than creating a general, one size-fits-all marketing strategy, advertisers and marketers can reach individual segments of their customer base. So instead of flooding all customers with the same offer, marketing teams can create personalized offers that keep the customer engaged and satisfied with the product.
An integrated approach to customer satisfaction
In an article entitled ‘How Your Supply Chain Benefits From IoT’ , Glenn Johnson, Senior VP, Magic Software Enterprises Americas, describes a scenario where IoT platforms can be integrated to provide a seamless customer experience. He says:
“Imagine your company bought you a mobile phone four years ago, and the charger is failing due to a badly worn cord. The mobile phone detects the intermittence of the electrical signal and sends an alert to the integration platform, which routes communications to the e-commerce, PLM, and ERP systems.
Your company's purchasing agent then receives a replacement order form automatically from the marketing automation system, and the product manager receives data in the PLM system informing a decision to improve future models. The e-commerce system receives the approved order, and the integration platform triggers the ERP system to record the transaction and the logistics system to ship it to your office.
You receive the package with a message, "Your mobile phone charger is about to fail. Here is the replacement." Upon delivery confirmation, the integration hub then triggers the CRM system to send you a thank-you note for the order, and records responses to a customer satisfaction survey.””
Conclusion
It’s a safe bet that business owners will want to improve the quality of their products and their customers’ experience in purchasing them; these factors will improve reputation as well as profitability. This article has shown how they can achieve both by adding IoT capability to their supply chain. Using sensors for track, trace and environmental condition monitoring will ensure users enjoy timely delivery of the right product in good condition, while ongoing monitoring and feedback after delivery will give suppliers deeper insight into users’ experience with their products and transactions, and how these can be improved.
References
https://www.entrepreneur.com/article/298464
http://diginomica.com/2016/09/26/transforming-the-supply-chain-for-better-customer-experiences
http://forwardermagazine.com/ask-the-experts/smart-manufacturing-the-connected-supply-chain
Swisslog-unveil-Asias-first-AutoStore-automated-warehouse
https://www.ibm.com/blogs/internet-of-things/iot-tracking-solutions-blockchain
how-the-iot-is-shaping-the-future-of-customer-experience-and-product-development
http://www.inboundlogistics.com/cms/article/iot-in-the-supply-chain
The IoT’s impact on supply chain management. Date published: 1st November 2017 by Farnell element14