The IIoT Will Have a Transformative Impact on Plant Maintenance
Profound changes lie ahead as the IIoT drives the shift from reactive to predictive maintenance
Plant maintenance has often been a source of untimely, expensive and unplanned equipment downtime. Preventive maintenance, managed by a computerized maintenance management system, has been a much better alternative to reactive, "breakdown" maintenance, but has not always been the cure to failures and production downtime. A solution that’s on the horizon, which promises to combat the high cost of plant maintenance, is predictive maintenance, a radically new form of maintenance that is enabled through implementation of the Industrial Internet of Things (IIoT) systems at manufacturing facilities.
From Preventive to Predictive Maintenance
There are many differences of opinion in the manufacturing industry with regard to the value of the Industrial Internet of Things. The on-going debate on the value of IIoT has frequently reduced the problem to corporate buy-in and capital investment, yet often overlooks its usefulness in the area of plant maintenance, which can amount to about 20% of operating expenses and between 4% to 7% percent of gross revenues for large organizations, according to the consulting firm Accenture. Without a doubt preventive maintenance has improved equipment life cycles and controlled the rising slope of capital costs. But the value of IIoT is multi-faceted; in the context of plant maintenance, it has the ability to take maintenance to a new level — well beyond a preventive style of regularly scheduled maintenance to an innovative, condition-based maintenance that is predictive in nature.
This move to predictive maintenance is expected to occur in the very near future as thousands of machine-based sensors feed data to industrial control systems in order to provide real-time information about both operational status and rule-based equipment conditions. Predictive maintenance is expected to significantly reduce unplanned downtime and eliminate many instances of catastrophic failures – those untimely accidents waiting to happen that kill productivity targets. But the promise of predictive maintenance can only be realized with the full scale adoption of the IIoT. Featuring more complex hardware and software as well as many I/O sensor networks, the IIoT poses a wholly new set of implementation challenges.
The Challenges of Implementing IIoT
Security, interoperability and connectivity are often cited as the three major obstacles to implementing IIoT. A lack of security for critical infrastructure is a risk to operational performance. A lack of standardized protocols for industrial networks can pose significant limitations on how to get gear from different vendors “talking” to one another. Since industrial processes operate in real time, the need for time sensitive, low latency and high reliability networks that connect massive wireless I/O to the controller is another important challenge that cannot be underestimated.
Beyond the considerations of data security, interoperability and connectivity is the I/O itself. One fact of life (and wireless sensor network maintenance) is that the life expectancy of sensors is uneven. As machine-level devices, IIoT sensors endure a significant amount of environmental exposure and stress that isn’t experienced by data processing equipment housed or co-located in an environmentally controlled data center. And sensor networks used in the IIoT will be huge – 20,000 to 50,000 at large facilities.
The maintenance of such a large I/O would likely be unmanageable without making communication down to the sensor visible – a critical need for the success of the IIoT. This is why the IO-Link standard is so important to implementing the IIoT and achieving the holy grail of plant maintenance – predictive maintenance.
Maintaining a Large I/O Demands Sensor Communication
Maintaining a large I/O starts with making communication down to the sensor visible. This is one of the goals behind the IO-Link International Standard (IEC 61131-9). What is IO-Link? In brief, it is the first I/O technology for communicating with sensors and actuators to be adopted as an international standard (IEC 61131-9). Technically speaking, it is a fieldbus and vendor-independent communication standard. Since IO-Link compliant devices can provide information about their status, they can be deployed to help reduce downtime because they can notify plant operators of faulty components in real time. As a result, the frequency of sudden failures can be drastically reduced.
IO-Link allows consistent communication between sensors/actuators and the controller by providing access to all process data, diagnostic data, and device information so corrective maintenance as well as the scheduling of preventive maintenance can be optimized. IO-Link can minimize the risks of catastrophic failures and reduce the efforts needed for troubleshooting equipment problems.
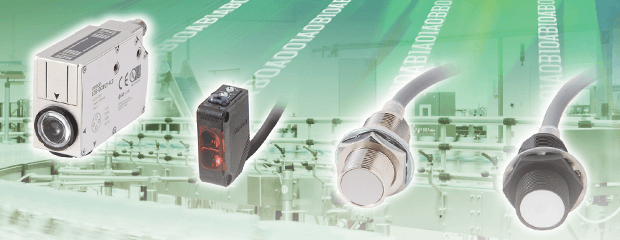
Omron’s IO-Link compliant products can make sensor process and diagnostic data, as well as device information visible in order to help reduce maintenance downtimes, eliminate frequent and sudden failures, and improve the efficiency of production changeovers.
With IO-Link, the last yard between the sensor/actuator to the fieldbus or controller becomes communication-enabled. The parameters for the actuators and sensors can be stored in the controller and automatically transferred when the unit is replaced. It allows the detection of wiring cable disconnections and errors. IO-Link can also help improve system commissioning and changeover efficiency by checking identifications in batches. This is especially useful when I/O checks for any of the thousands of sensors installed on a production line must be performed.
IO Link Helps Realize the Promise of IIOT
The importance of the IIoT to the continued success of the manufacturing industry is no longer in the experimental arena. The majority of manufacturers are already at some stage of investment in IIoT technology. But the broad scale adoption of IIoT and the benefits it promises to offer – from predictive maintenance to high productivity and ROI – will depend on the engineering of a coordinated set of solutions, of which, IO-Link compliant devices will play a key role at the sensor/actuator level.
What do you think about IIOT and the move to predictive maintenance? Share your thoughts on our IoT Community hub.